Under the course MECH4412 (Design and manufacturing), the hands-on project is an important element which allows the students to develop hands-on skill and problem-solving technique. In the last academic year, the project title was “An automated storage and retrieval system (ASRS)”. ASRS consists of a variety of computer-controlled systems for automatically placing and retrieving loads from defined storage locations. The benefits of an AS/RS system include reduced labour for transporting items into and out of inventory, reduced inventory levels, more accurate tracking of inventory, and space savings. Items are often stored more densely than in systems where items are stored and retrieved manually.
In this project, the students are required to build a plugin system onto a framework which aims at storing and retrieving A4 boxes (219mm x 312mm x 269mm) on a standard 4 levels shelf (1.3m × 1m × 0.4m), which can hold 12 boxes as shown below. The weight of each box is about 1kg. The system consists of an interface, controller and a transport platform. The system should get the box location from the user and be able to store and retrieve the specific box from the storage shelf. Safety feature should also be integrated to avoid failure, e.g. overweigh and collision.
There were 79 students participated in this project. They were divided into 10 groups of 8~9 students.
The competition was held on 30th April 2019 & 2nd May 2019. Ten groups of students demonstrated and explained their design to the supervisor. All teams could complete the mission successfully. Among all the teams, the prototype of group 5 could store and retrieve storage in two opposite storage shelf with the fastest time, and hence group 5 was the winner of the competition.
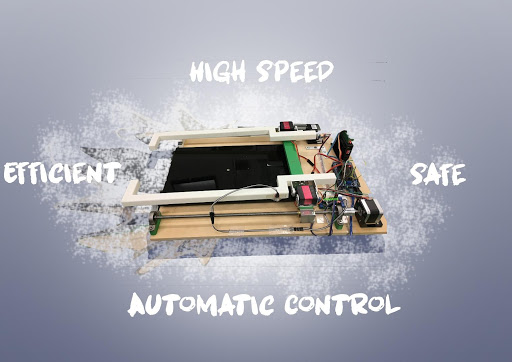
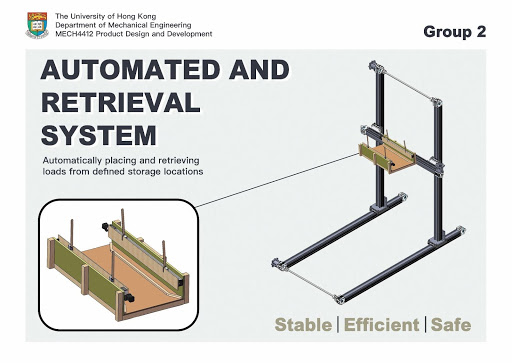
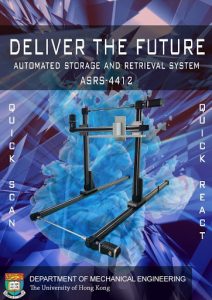
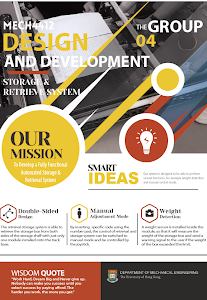
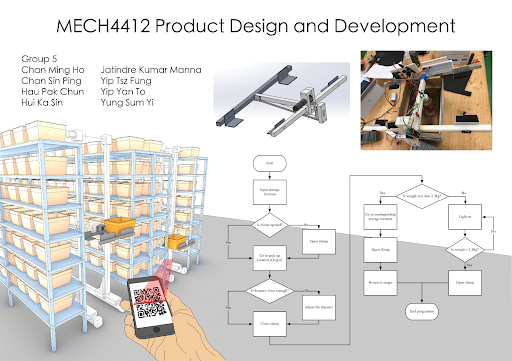
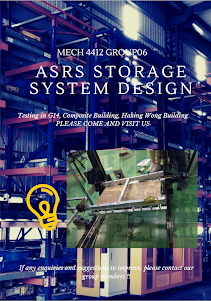
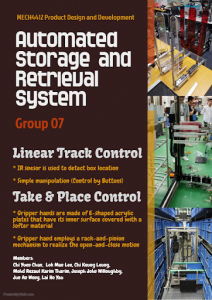
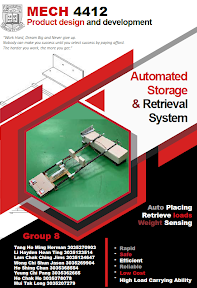
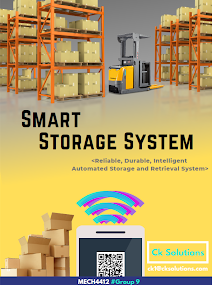
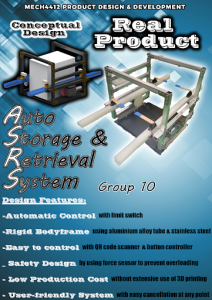
During the two days competition in April & May, different teams and members communicated and exchanged ideas with each other, say, the design concerns, store and retrieve mechanism and efficiency of their design in terms of speed and reliability. Students recurrently went through a series of brainstorming sessions, rapid problem-solving sequences during the competition.
In the competition, all the groups demonstrated their design successfully. Although some groups had better performance than others, their enjoyment on completing all the mission was beyond the match ranking.
After the competition, the summer internship (TA position) were provided to year 3 potential students for implementing potential designs during the summer. One capstone design project team will be established for developing a workable 1: 1 prototype for the InnoWing.
This project allows our students to work through the fundamental engineering design process and to integrate what they have learnt in different courses into a practical task. It helps the students to develop a deep knowledge instead of an exam-based memory in different course subjects. The project also enhances the relationships between me and the students.
A fresh design challenge is set for every year of the course MECH4412. It allows the students to be innovative in resolving engineering problems. It also lets our students to aware of the importance of reliability study in engineering design, especially in real-life application and competition. Accordingly to the Murphy’s law, “If something can go wrong, it will.”, it is true in many competitions.
Albert Einstein quoted: “Everything that can be counted does not necessarily count; everything that counts cannot necessarily be counted”. Although the project contributes only 30% to the overall marks in the course and the work loading is comparatively very high amount other courses, it is a valuable chance for the students to show their talent in their study.
“The project of constructing a functioning ASRS model was challenging and required many days of planning, prototyping and redesigning to execute successfully. The project allowed the team to learn the various aspects of the course in a practical setting, showcasing the real-life challenges associated with creating a functioning system and the importance of following the various design principles and guidelines taught over the course of the semester. These learnings allowed the team to successfully complete the ASRS model and carry out a demonstration of the same on the first day of the competition itself. The team is certain that its learnings and growth as engineers during the course of this project will serve them well as they move into the engineering industry in the coming years.“
Group 1 sharing
“The scaled-down ASRS was successfully designed in terms of automatically placing and retrieving loads from defined storage locations. The combination of customized software and hardware enable the control of moving the designed wooden platform, retrieval system and the accessories parts which help to get the works done. It achieved all tasks required in the competition, including transporting the commodity to a specific location and retrieved back. The safety precautions also performed its function to protect the system when there are emergency issues. However, the material constructed the platform engaged unexpected swelling and bending due to humid weather and heavy load respectively. Hence, the change of material is necessary for the system. Advancement of the coordinate system and secondary arm structure are also the focuses of future direction. Wish that a two-sided ASRS, which is developed on top of this project will be applied in the future, that can improve the storage and retrieval efficiency and contribute to the logistics industry.“
Group 2 sharing
“In this project, a prototype of automated storage and retrieval system (ASRS) was developed for the upcoming Tam Wing Fan Innovation Wing. Existing ASRS were first reviewed to gain knowledge of the system. Then, the system was designed, built and tested based on the situation of the Innovation Wing.
The system’s storage and retrieval mechanism adapted a forklift structure, which is paired with pallets placed under storage items. Sensors were integrated into the system for better control. The items were placed or taken according to the QR code scanner, which contains the information of storage location. Information from the different sensor was inputted to the programmed Arduino board for control. During official testing, it was proved that the produced prototype was capable of storing and retrieving items automatically.
With the system’s success, it can potentially be developed into the actual ASRS for the Tam Wing Fan Innovation Wing. Moreover, it can even act as the blueprint for future ASRS developments in HKU or other places with similar uses.
While the current developed system is capable of performing the fundamental functions of storing and retrieving items automatically, there are some shortcomings. As the prototype has to be scaled up for actual use, there are concerns of how the system can operate in an array of storage racks. Also, it has to be further developed to improve user experience as the prototype has fallen short of developing this aspect.
It is recommended that, in the future, more trials can be conducted to test for irregularities in the system. Furthermore, as mentioned in the previous paragraph, user experience has to be taken into consideration for further development. Surveys can be performed, as well as inviting occupants to test the system. It is certain that the system will be more user-friendly after additional developing.“
Group 3 sharing
“ASRS (automated storage and retrieval system) is a common system found in the warehouses of manufacturing, distribution, retail and courier industries. To facilitate the design of an ASRS that will be installed in the new Innowing by the Faculty, we were asked to prototype a mini ASRS system. In this project, we have to design and build a plugin device onto the predesigned crane and programme the entire machine using the Arduino platform. Please note that due to time constraint, a lot of compromises has been made to our design to shorten the design time and maximizing the window for testing.
In this project, different functionality was developed to facilitate the user convenience. Our system consists of a built-in power supply, a monitor, a controller, a number pad and a memory unit. Therefore, the system can operate entirely on its own without requiring to be connected to an external power supply and computer system. Even during a power outage, the memory of the system would not be lost. It is also not necessary to plug the system to a laptop to run. Our system consists of a pair of cranes which can extend over to both left and right shelf, making two-way stock loading and retrieving possible.
Our system can operate under both auto or manual mode. While auto mode can load or retrieve stocks automatically, manual mode allows user/maintenance staff to override the auto mode and operate the system under manual control in case of emergency or system malfunction. Our system is able to store the status of each storage space. Therefore it is able to find a vacant space automatically and does not require the user to input which space does he/she wish to store the box into. The system will terminate any loading action when the shelf is fully occupied. Our system consists of a weight sensor under the loading platform which detects the weight of the loaded stock. If the weight of the loaded stock exceeds the system limit, the loading action will be terminated. This mechanism enhances the overall safety and stability of the system. Our system has a straightforward user interface as demonstrated in the demonstration session. No additional instructions are required. The system works much like an automatic station locker in some main train station.“
Group 4 sharing
“In the competition, our group was able to store the boxes on and retrieve them from both the left and right storage racks. In one of the retrieval trial, the command was set to storage mode by mistake, causing one abnormal retrieval process. All the other trials were successful and the boxes were stored and retrieved without any deformations and misplacement.
The final version of the clamp was developed after three major modifications, which involves changing the clamping mechanism to lifting, modifying the structure of the storage box and simplifying the clamp structure.
The final product is the simplest prototype amongst all the designs and it is the cheapest model as well. Although the total weight of the finalized clamp structure is heavier than the first prototype by 40% due to the replacement of the 3D printing components with aluminium rods, the lifting process is simpler and the design is easier for alignment.
In terms of mass production, the finalized design is significantly lower in cost than the previous two models as the materials are mostly aluminium rods, which are both cheap and readily available in the market.
To conclude, our group was successful in achieving the goal of ASRS. There is still some room for improvements such as using weldment for combining components and the modifying the structure of the storage box..“
Group 5 sharing
“Automatic Storage and Retrieval System (ASRS) has simplified warehouse storage and retrieval process and improved working efficiency. To implement such technology in the future InnoWing storage area, this project proposed a prototype ASRS system.
The track control algorithm used IR sensor and black cardboard to locate the cargo position. The gripper design incorporated DC motor for open and release mechanism. The gripper mechanism was mounted onto acrylic plates and bolted onto the track mount. It was also planned to include force sensors, contact sensors, and ultrasonic sensor for precise gripper control. However, the actual product did not include those sensors due to calibration and testing issues.
The proposed prototype was tested during the demo session which showed positive results. To further improve the proposed design, it was suggested to expand the current user interface with the use of QR codes for simplified input. Extra turning mechanism can also be installed to allow the gripper to reach shelves on both sides of the track. Future projects are expected to refine the concepts tested in this prototype to achieve a fast and accurate Automatic Storage and Retrieval System.“
Group 7 sharing
“To conclude, the Automatic Storage Retrieval System (ASRS) provided great assistance in storing/retrieving items in the warehouse with the help of computer software and robotics components. It acts as an important role in enhancing efficiency and promoting ergonomics.
After testing, the product was found to perform that aligns with the expectation which able to store and retrieve the 1kg paper box with to defined location. However, limitation and difficulties exist in this project. Firstly, the weight sensor had poor accuracy in measuring weight data which can be improved by a more sound design which taken all parameters into account. Secondly, hardware can be improved by selecting a suitable material and modifications of structural design to strengthen the structural strength and loading withstanding ability. Lastly, the accuracy of locating the paper box could be enhanced by giving an explicit programming code.
The success of the design marks the milestone of the success of launching the actual ASRS in InnoWing. Furthermore, it also helps to promote a similar technology apply in a warehouse or another storage system in the future.“
Group 8 sharing
“In the end, our ASRS successfully accomplished all the project requirements. The storage and retrieval processes were very smooth and accurate, though the actual running speed of the pallet jack was slower than our anticipated value. The speed is tuned down by 30% on purpose to prevent step skipping due to reduced motor torque at high speed. This problem can be largely attributed to the hardware limitation of the DMA860H stepper motor driver provided, which only has a maximum micro-stepping size of 400 pulse/rev. Assuming that the motor driver cannot be changed, one possible solution to this problem is to include a speed-increasing gearbox to raise the top speed of the jack while maintaining a reasonable amount of torque output. However, the number of components and complexity of the overall design will increase drastically, possibly lead to a premature failure of the mechanical system. Further research and prototyping are required to overcome such a challenge.
The Android-based controller application turned out to be a very suitable platform for implementing the MMS. The excellent compatibility of Android operating system allows our MMS to be used on virtually any Android devices. of our clients is one of our prioritized design concerns. Smartphones nowadays are equipped with all the modules needed in our project, including QR scanner, Bluetooth and storage memory. All the controlling tasks can be easily done on the Android controller app with just a few clicks. Furthermore, the MMS can be further expanded to the real, large-scale ASRS without significant re-modification.“
Group 9 sharing
“An ASRS system was designed and built in this project. This designed device was a scaled-down model of a real ASRS system using in storing rooms or areas. The task of this automatic-controlled device is to store and retrieve the items on the shelf.
The main focus of this project is to design the mechanical plug-in device, which is connected to a linear track base to form an ASRS system. By using various manufacturing methods and different selected materials, the mechanical plug-in device was built. It was controlled by an Arduino program which was also designed by our team. The Arduino program was written in C language. By connecting the hardware components with the Arduino DUE board and MEGA 2560 board, and uploading the designed program to the boards, the device was able to perform the tasks.
Though the functions could not be carried out in a single program, our designed ASRS system successfully performed all tasks. Other than normal components which were installed to finish the tasks, there were some safety precautions that we installed on the device to protect the device from serious damage and losing control. During this project, we encountered lots of challenges and difficulties. Luckily, we solved some of the difficulties and figured out optimal solutions for them. However, some defects were discovered in our device. These flaws were discussed and should be improved for similar projects in the future.
In conclusion, our team has successfully designed and built a scale-down ASRS system. The system could be controlled by our designed Arduino program to complete the items storage and retrieval tasks.“
Group 10 sharing
This article appears in the news from the HKU Engineering Faulty website
The “Design, Build and Fly” Team of Department of Mechanical Engineering participated in the “23rd AIAA Design Build Fly Competition” in the U.S.A. and ranked 13th among 104 eligible teams, which is the best ever result of Hong Kong teams since 2013.
The team, supervised by Dr C.K. Chan, comprised five mechanical engineering students Ng Ka lok Kelvin, Yip Tsz Fung Edmond, Ng Cheuk Long, Ng Cheuk Yin Martin and Mok Siu Hei. They took part in a 4-day competition at Tucson International Modelplex Park Association (TIMPA) Airfield, Tucson, Arizona of U.S.A. from April 11 to 14 2019. With the theme “Aircraft Carrier Operations” in this year’s contest, the team submitted a design report and was shortlisted, ranking 9th and became one of the 77 competing teams from top universities all over the world.
Each team is required to complete a timed ground mission demonstrating full carrier operations and capable of completing three missions, including Delivery, Reconnaissance and Attack. The team successfully completed all the three missions and was ranked 13th in the competition. This is the best ever result among the teams from Hong Kong and is the best result in East Asia.
“It is our first time joining the most influential aircraft model competition in the U.S.A and we are very delighted to get the best ever result among the Hong Kong teams,” said by Professor Christopher Chao, Dean of Engineering, “In HKU, we emphasise experiential learning and we always encourage students to actualise their idea through hands-on projects in which they can “learn by doing”. It definitely sets a good example for their fellow classmates.”
Dr C.K Chan, the supervisor of the team, felt proud of the students’ achievement and said, “This competition meant a lot to the students. It is meaningful and eye-opening for the students to compete and communicate with other teams from top-notch universities on-site. We must thank the University and family members for their support, without which we would not be able to succeed.”
The “Design, Build and Fly” competition was organised by the American Institute of Aeronautics and Astronautics (AIAA) in which students are required to design, fabricate and demonstrate flight capabilities of an unmanned, electric powered, radio-controlled aircraft representing real-world aircraft and aerospace design challenges. It is the most influential aircraft competition in the States and attracts teams from renowned institutions such as MIT and UCLA to join the competition.
More details of AAIA Design Build Fly Competition 2019: https://www.aiaa.org/dbf
Media inquiries:
- Dr C.K. Chan, Department of Mechanical Engineering, HKU (Tel: 3917 8554; Email: ckchan1[at]hku.hk) or
- Ms Celia Lee, Faculty of Engineering, HKU (Tel: 3917 8519; Email: leecelia[at]hku.hk)