Formula Student UK is an educational engineering competition. The competition aims to develop enterprising and innovative young engineers and encourage more young people to take up a career in engineering. Formula Student UK 2020 will be held at Silverstone Circuit, Towcester, UK. HKU team will join the Electric Vehicles Class 1 Division competition.
Members of the team will get the opportunity to design and build a formula style racing car from the ground up. The comprehensive characteristic of the competition requires members to fully understand how engineering interacts with business environment. It allows engineering students to put their academic knowledge into practice and further prepare them for their future engineering career.
Due the outbreak of COVID‐19 pandemic around the world, the live event of the Formula Student (FS) 2020 at Silverstone UK has cancelled. The FS2020 competition becomes a completely online event. HKU Racing took part in over 400 virtual presentations for the Business, Cost, and Manufacturing and Design events.
Besides, the weekend’s traditional Dynamic Events were also taken online for the first time, with Lap‐Time Simulations using Multi‐Body Dynamics Model and recreations of the courses used at Silverstone. HKU Racing had the opportunity to test their driving abilities in EXPERIENTIAL LEARNING FUND online races using the Assetto Corsa simulation software.

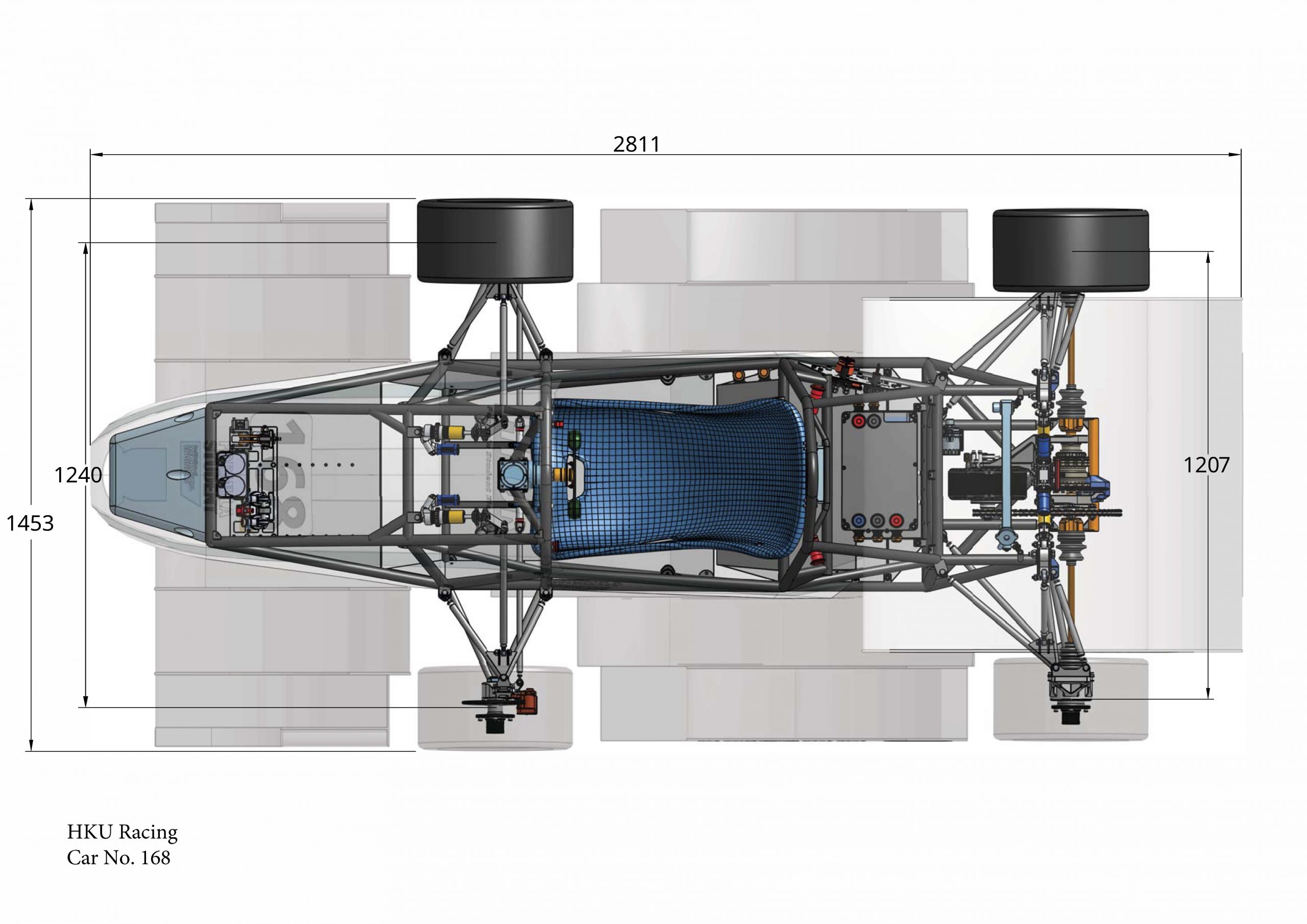
- 2nd in business plan presentation
- 12th in the overall result
- Prototypes of key components/parts of the formula student EV
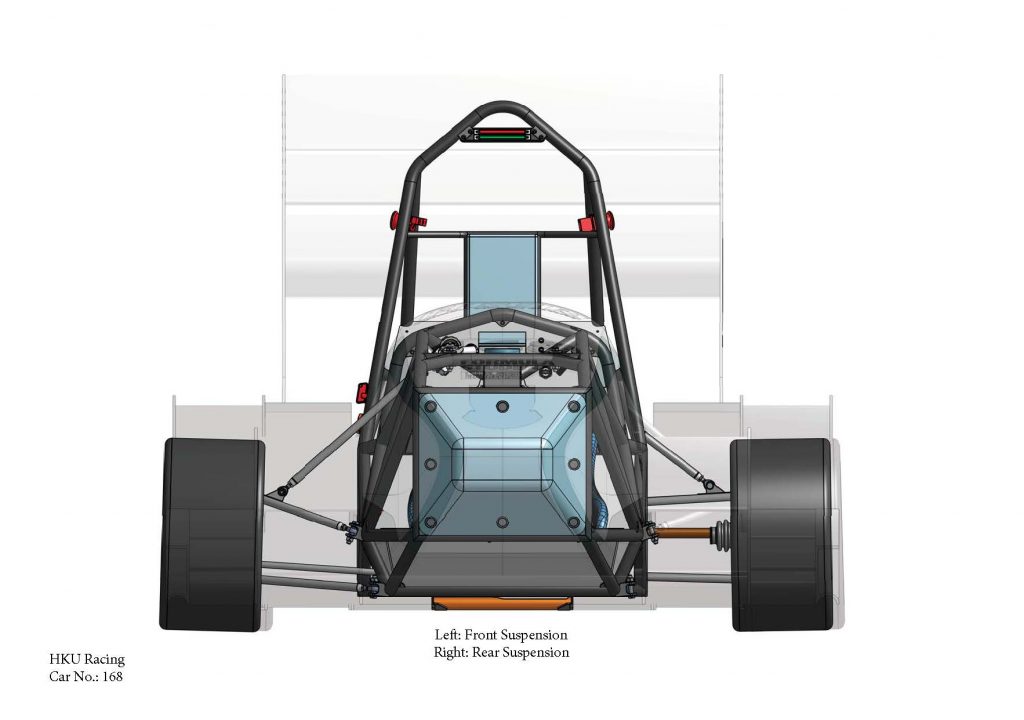
- Project report for Formula Student UK competition
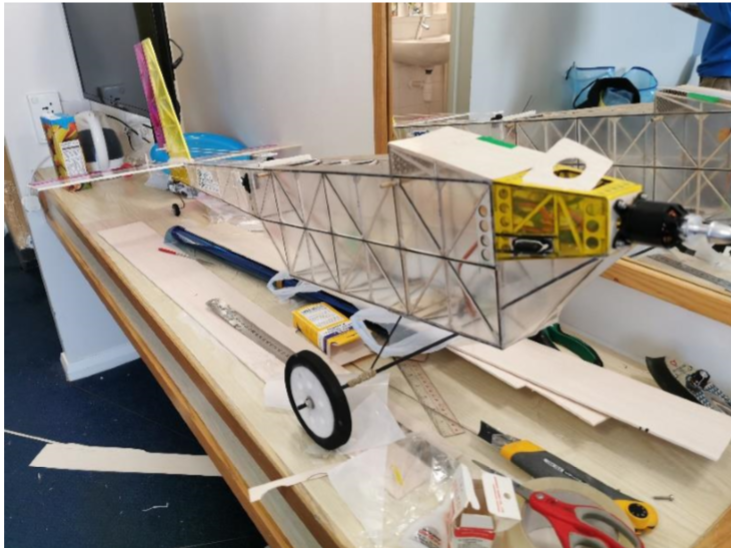
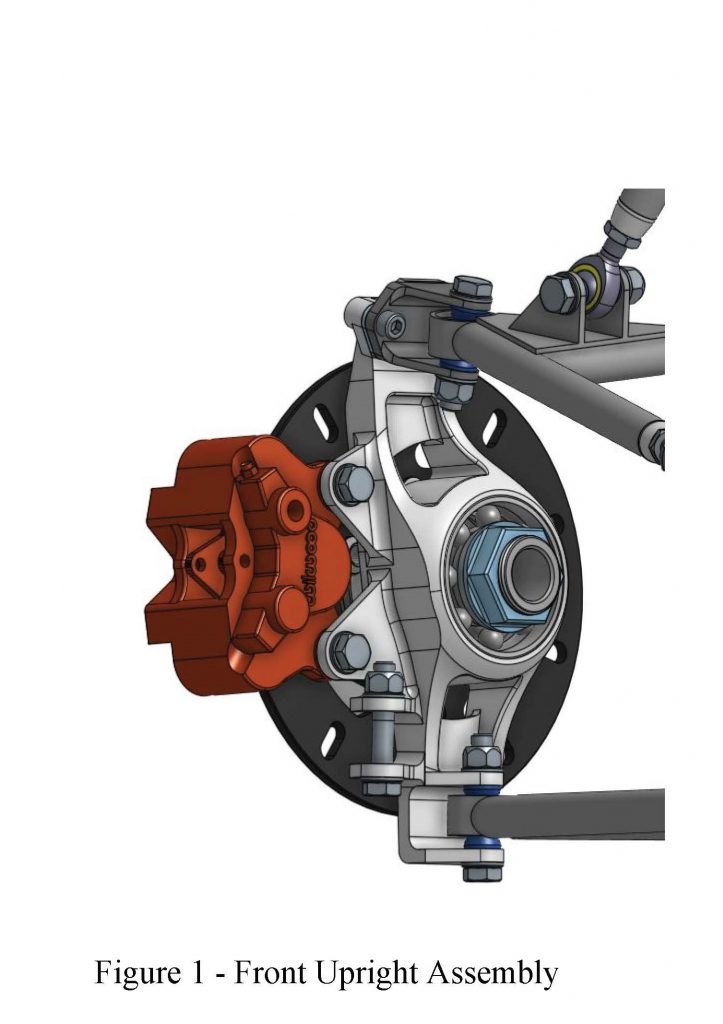
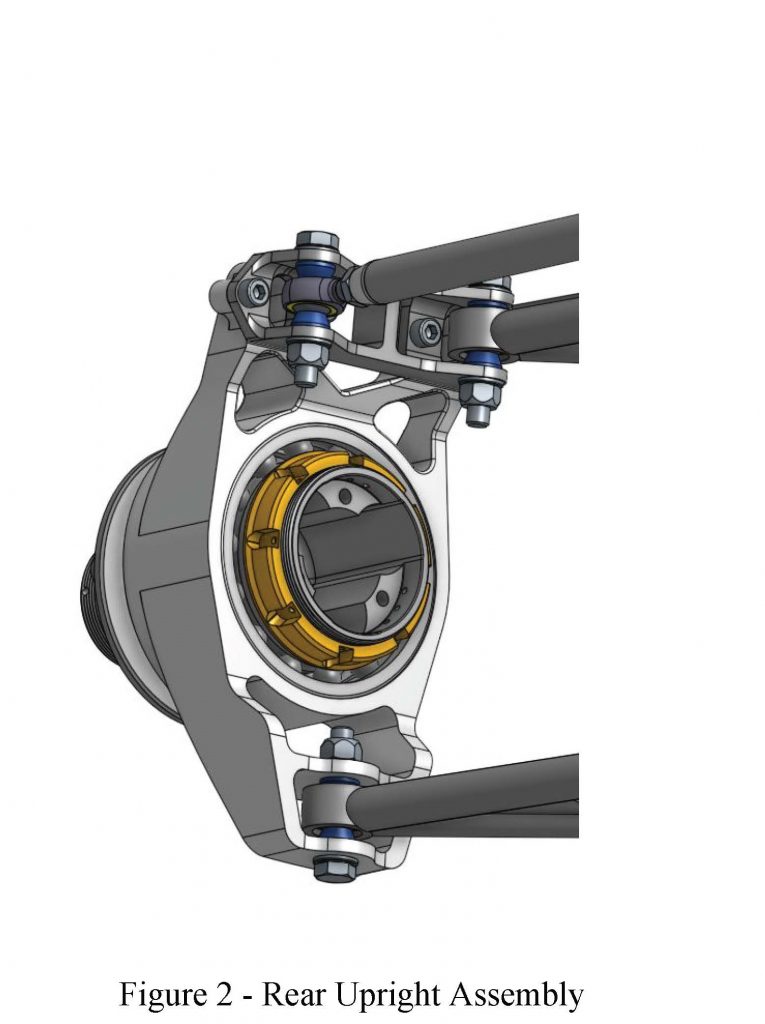
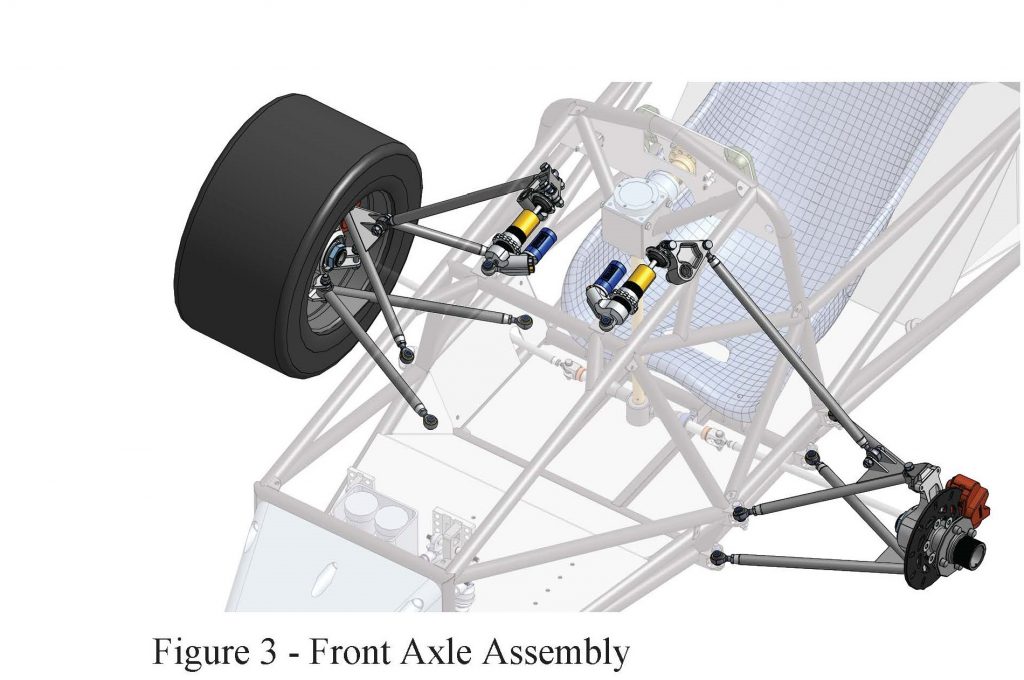
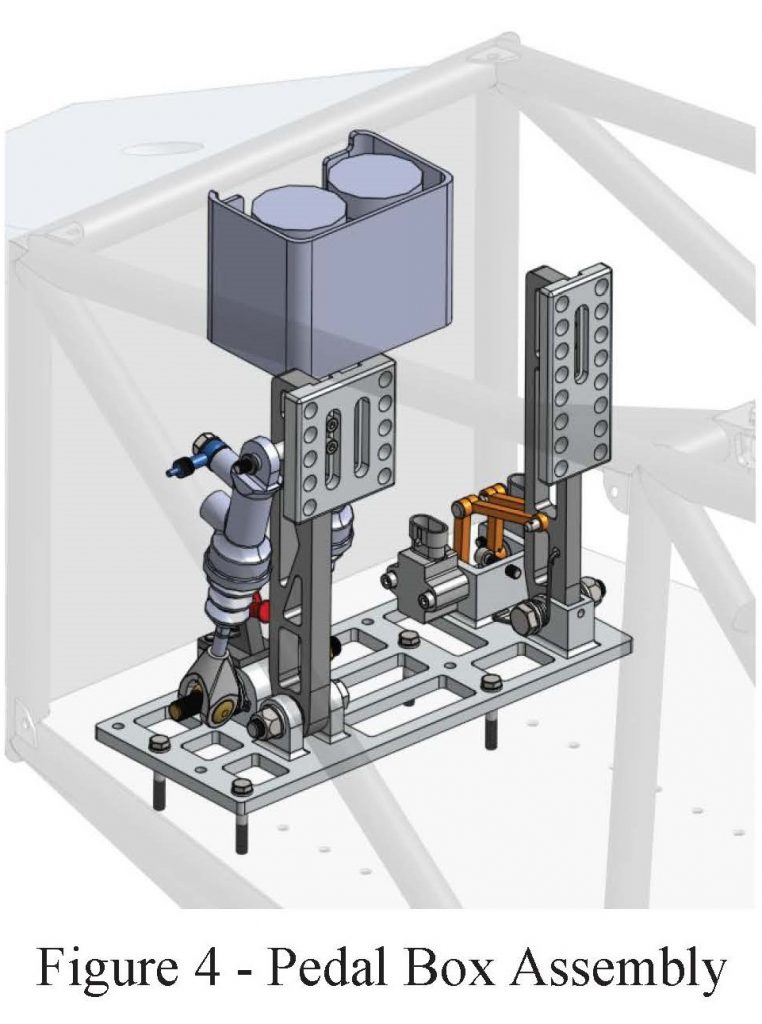
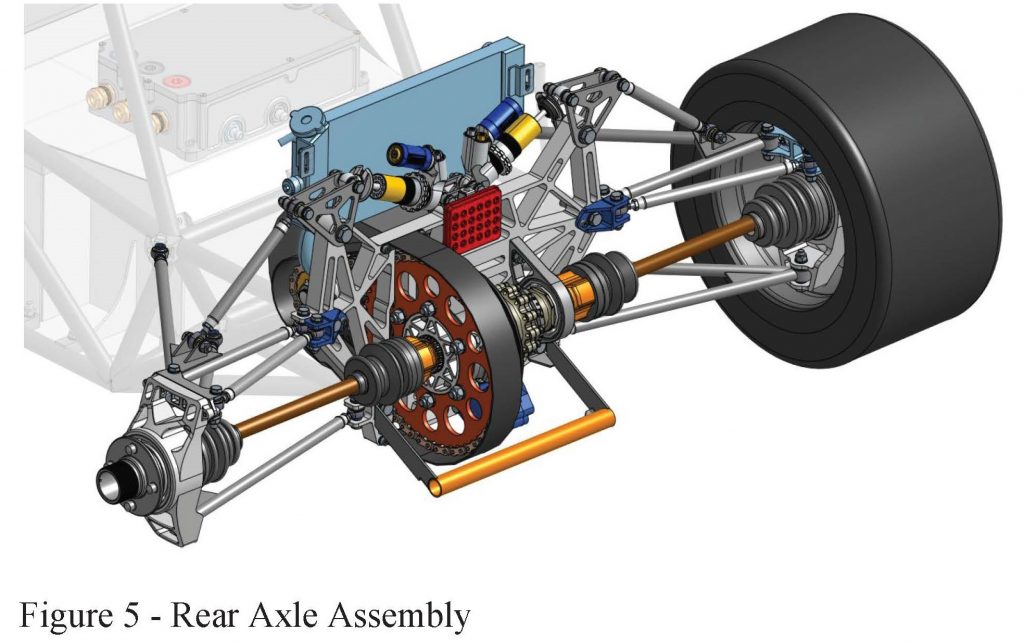
Introduction
This is the second year HKU Racing participates in FSUK. Taking experience from our Class 2 entry in 2019, we have designed a production-ready class 1 contender that focuses on reliability and manufacturability. Improvements have been made to provide better performance and better packaging. In this design report, we will discuss our design process and our plans to bring the vehicle into operation in a reliable manner for FSUK 2021.
Overall Vehicle Concept
As a first-year team in class 1, we value reliability over performance. We believe experience is the key to improving performance. By building a reliable contender we build up experience to improve in the future. In addition, the high rate of failure to complete endurance events gives us an advantage over our competitors. With high reliability, our design will also appeal to our frictional customers as it means reduced running costs and frequency for repair. Our vehicle has adopted an electric powertrain. We see electric transportation as the future mode of transport.
Moreover, our university shares this same vision and is supportive of electric powertrain development exclusively. With an electric powertrain, many efforts have been put into minimizing weight in all areas of the vehicle to compensate for the added weight. Since EV powertrain is sensitive to power efficiency, aero development has focused on reducing drag to downforce ratio. We have achieved this by focusing on the development of the undertray and diffuser. The suspension has been designed to integrate the need for larger ground clearance at the rear and rear bulkhead cross-section required by the powertrain. In our simulation, our vehicle’s weight is 200kg, acceleration event completing in 4.6s, and achieving a maximum lateral acceleration of 1.5g.
Structural Design
Spaceframe is chosen for its ease of design and manufacturability compared to monocoque chassis. AISI 4130 Chromoly steel tube is used due to supplier limitation. The rear of the chassis adopts an aluminum plate for mounting drivetrain components. This is done to eliminate bad load paths that put steel tubes in bending. For the manufacturing, TIG welding is used with ER70S-D2 filler rod, which can give better weldment than using MIG.
Suspension has adopted a double-wishbone pushrod system with converging unequal length wishbones for both axles. A pushrod system has been chosen to locate the dampers at an inboard position. It cleans out the airflow and reduces drag, which is beneficial to the energy efficiency in the powertrain. Top-mounted dampers allow for easy access to make on track suspension adjustments. The converging wishbones are designed to induce camber recovery during roll movement as formula student tracks are composed of smooth surfaces, the trade-off of poor camber control during bump has a small probability to upset the wheel’s contact to the road surface. At the front, due to the limitation of chassis width by the rules, the short and unequal length wishbone set up will aid the camber recovery feature. The added benefit for the unequal length design allows us to have a stable roll center. We are able to minimize the roll center movement in the vertical to 9mm at the front and 0mm at the rear at up to 3.5 degrees of roll. Roll centers are carefully designed with optimum handling in mind. The roll center at the front is at 42mm and the rear at 51mm above the ground plane. The lower placement of the roll center at the front is to create a forward inclined roll axis, producing neutral handling. The spread of the wishbone at the front has been maximized to reduce the loading in the wishbone member. This removes the need to have larger components and minimize the forces transmitted to the chassis.
At the rear, the wishbone spread was dictated by the placement of the rear axle. Together with the powertrain, we designed the new rear end with the focus on allowing sufficient space for the diffuser, shortening the chassis and maintaining minimum angle for the CV joint when the vehicle is in static. Much care has been put into the design of wishbone to avoid rod end in bending situation, with correct usage of rod ends and spherical bearings, the chance of mechanical failure has been minimized. Toe compliance is also limited by maximizing the toe base on both front and rear upright. Finally, FEA was used extensively to maximize the strength to weight ratio in components such as the upright.
While conventional hydraulic disc brakes are used at the front wheels, the rear brake adapts an inboard system. This can reduce the unsprung weight to improve handling. The rear brake disc is mounted on the differential, same as the drivetrain input.
In aerodynamics, we use CFD simulations and lap time simulation for validation and design of experiments together with optimization algorithms to take the guesswork out of the R&D process. Front and rear wing uses airfoil E423 and S1123 respectively. Aerodynamic balance is achieved by first designing the rear end of the vehicle. The downforce generated in the undertray reduces the dependence on the rear wing thus reducing drag figures. The undertray has 2 Venturi tunnels, intake air from under the side plates between the rear wheel, creating a low-pressure area.
Powertrain
In contrast to combustion cars, electric powertrain has many options in motor placement and wheels to be driven. Compared to a 4WD system using hub motors, using a single electric motor paired with a differential has lower cost and does not require advanced knowledge in programming torque vectoring. Therefore, the latter is chosen for its simplicity and a higher chance of producing a reliable first-year car. The EMRAX 208 is selected for its high efficiency and good reliability among formula student teams. The medium voltage version is chosen together with the Cascadia Motion PM100DX motor controller for its maximum 400V input. This setup can draw close to the 80kW power limit, which can achieve 4.6s in the acceleration event according to our simulation.
The accumulator has to be custom designed as there is no market available solution for formula student specification. The lithium cell selection is influenced by our sponsor, which is also our battery supplier. The 7.4 kWh capacity is estimated using OptimumG lap simulation and referencing other established teams. Lastly, the voltage and amperage value are determined by the motor controller maximum voltage input.
The accumulator is the heaviest component of the car so it is mounted right behind the driver for better mass centralization. The motor and drivetrain are mounted at the end of the car. Considering it is difficult to achieve a good load path using steel tubes in the frame, a 25mm thick aluminium plate is designed to mount the motor and differential. The drivetrain forces can be balanced and driving force can be transferred to the frame more effectively. This also allows for a tighter packaging and therefore reduces the overall length of the car.
Overall Planning
Our team operates at 3 levels. The 6 divisions, suspension, aerodynamics, powertrain, driving input, electronics are responsible for the development of respective components on the vehicle. Their division leads together with an electrical system officer and treasury reports directly to the team captain. Close communication between division leads and team captain ensures the design direction is on track. Treasury works close to the individual division on their planned spending and updates the team captain with finances in the team. The electrical system officer works with our team’s electrical system advisor to overlook the development of electrical systems. The team captain is responsible for sponsorship scout, negotiation with the university for funding, as well as project planning and execution.
Experience in the design of our 2019 contender tells us the importance of CAD files versioning and virtual assembly management. Therefore we have switched to Onshape from Solidworks for most of our CAD design. With Onshape, it makes sure everyone is working on the latest version of the design. The software allows for real-time collaboration, especially helpful when working from distance. Onshpe’s integration with Simscale, one of our sponsors, lets us run FEA with cloud computing. This alleviates the need for more advanced computing hardware.
Our team completed the design phase in December of 2019, we have moved on to the manufacturing phase since January 2020. The project plan was to have the vehicle completed within 4 months of manufacturing by the end of April. With running tests taking place from May to mid-June and we will have our vehicle shipped to the UK. To cope with the current global pandemic, a revised plan is now in place. The situation affects us in a few ways. Social distancing rules mean that both university staff and team members are required to work in a reduced capacity. This has slowed down our capital approval process and purchase order issuing process by the university. And members of the team will have to adapt to working from distance. With most of our components supplied from China, some from Italy and America. The manufacturing and shipment of our components have been seriously delayed.
In the revised plan, we will complete the assembly process during the summer break. To take advantage of the extra preparation time, we will focus our effort on improving the reliability of the vehicle and the manufacturing of composite components. Vehicle testing will commence right after assembly with focus on powertrain performance and reliability as well as vehicle set up. Data acquisition systems, such as linear sensors and strain gauges will be installed. Over the months that follow, the vehicle will be tested repeatedly. Driver training will proceed in parallel to extract the best performance out of the car. Composite manufacturing was our biggest manufacturing hurdle in preparation for FSUK 2020. We will, therefore, be experimenting with different methods of mold constructions and layering techniques. When composite components are ready, vehicle testing will incorporate the new component and fine-tune the vehicle’s set up with a full aerodynamic package.
Manufacturing
Throughout the design of the whole vehicle, standard components and off-the-shelf market available parts are used where possible. This greatly reduces the cost to produce custom made parts and improve manufacturability. For example, rod end inserts and spherical bearing holders for wishbone construction are sourced directly from a bearing supplier. They are cheaper and have a faster turnover than custom CNC manufacturing.
In cases where custom parts are necessary, CNC processes are used. They provide more accurate results and faster turnover than manual processes. It can also eliminate the need for skilled workers which is hard to obtain for us. For example, steel tubes for the frame are laser notched and roll hoops are CNC bent. Machined parts are designed to be manufactured by 3 axis CNC machines, which is cheaper than 5 axis CNC machines and have better availability to us. Sheet metal parts are manufactured by laser cutting. It provides good accuracy and fast turnover at a reasonable cost. Low stress bearing parts such as small brackets are designed to be 3D printed using FDM machines. They are readily available and allow for rapid design iteration.
After completing the prototype, we expect some changes to the manufacturing process to accommodate a larger production volume. Custom machined parts can be made cheaper by reusing special fixtures and machine setup. For large enough volume, they could be manufactured by casting which will lower the cost per part. For weldments such as frame and wishbones, permanent welding fixtures should be designed for better repeatability.
Conclusion
Class 2 entry in 2019 gave us a solid base to improve on the design. HKUR01 focuses on reliability and manufacturability. The vehicle embodies the passion and dedication of our team.
The team will continuously develop the full scale vehicle and take part in the class one competition in 2021.
I would also like to thank the Tam Wing Fan Innovation Wing, Department of Electrical and Electronic Engineering and Department of Mechanical Engineering for their funding support.
I wish to express my deep appreciation and gratitude to our external advisor Ir Alexander T. S. Wong providing us with his expert advice. I would like to thank Prof. K.W. Chow, Dr. C. K. Chan, Dr. Match W. L. Ko and Dr. C. K. Chui for their assistance in this project.
I congratulate all the students on their remarkable personal growth and outstanding achievements in this competition. I have no doubt that everyone in the team will continue work hard and excel themselves to reach new heights of success in next year Formula Student UK 2021.
“This is my first year to take up great responsibility for HKU Racing in the FSUK 2020 competition. In last year, I only take up a small workload on the design of the car. This year, I am responsible for the braking system design and manufacture of the car.
Participating in such a huge international event on behalf of HKU is a wonderful experience for me. In Hong Kong, there are few chances for engineering students to work in the motorsport industry. The competition experiences enrich my understanding of the engineering theory behind a formula car. To make the best braking system design, I need a comprehensive knowledge of the structure of a vehicle. Therefore, I make a great effort in studying different systems inside the vehicle. It raises my interest in vehicle engineering.
Although the FSUK2020 changes to online competition due to the pandemic, I still find the experience fruitful. The judges of static events are nice and supportive. They give many positive feedbacks and comments for us to improve. From the comment of the design report, I can know the downside and potential issues of the design. Then, I can research and do simulations to further validate my design concept. This arrangement gives me an invaluable opportunity to learn effectively.
Other than the online static event, the dynamic event is also a special experience. Although we cannot drive our car on the Silverstone circuit, we still get an opportunity to race with other teams. In the virtual dynamic event, we can drive various race cars in different wellknown circuits and compete with other teams. Other than acquiring technical engineering knowledge, it is also important for us to keep the enthusiasm in motorsport.
Last but not least, our team gets the 2th in business plan presentation and 12th in overall result. I believe this is an acceptable result for the first-year team in the Class 1 event. Still, there is a large room for improvement in the engineering design and cost part. In the end, I would like to thank IMechE, all judges, and participating teams for continuously supporting the competition. I believe this competition is undoubtedly beneficial to engineering students.”
Tseng William, Team member
“This is my second year to participate in the Formula student event. Although we were not able to travel to the UK, I am still grateful to have this opportunity to show off my hard work with the virtual event that was being held this year. I am the team captain of HKU Racing and I am responsible for the suspension system design and manufacture of the car and focus on cost and manufacturing event.
Due to the current pandemic situation, it is very unfortunate that we cannot take part in the competition in the traditional way, driving the car we designed and competing against other universities from across the globe. The format for this year’s event is all virtual and the dynamics event is separated from the official ranking of FSUK2020. Meaning that only static event is counted for the official result and dynamics event will serve as a chance for teams to practice their analytic skills of setting up the car for various runs.
For static events we first pre-recorded the presentation and then followed by a live Q and A session. I think what is really interesting about this experience is that it is very similar to how engineers continue their work throughout this pandemic. Work from home arrangements meant that face to face meetings have gone virtual with all kinds of virtual meeting software. Engineers have to quickly adapt to this new setting and still communicate constantly with different stakeholders of the engineering project. In many cases, they also have to invent or create their own tool to better suit their specific requirements. And our team also have to adapt our knowledge from past year in a bit to extract the most out of this virtual format and effectively delivering all of our ideas to the judges. With this goal in mind we make extensive use of multi media and computer software for better illustrations to showcase our ideas in a more attractive and effective way. For example, we have dozens of animation and computer rendering of our design which all implemented into the presentation design.
One more unique features of this year’s competition is that we are given the opportunity to think about what we as an automotive engineer can contribute in helping the country to recover from this pandemic. Especially at the start of the pandemic where ventilator is in extreme shortage and every nation is scrambling to get their hands on more units. We were give the scenario and presented our way to use our “motorsport team” resources to help increases the production volumes of these ventilators and how we plan to operate with reduced working capacity. This is actually a real situation which many formula 1 team took action to help out the NHS.
Taking part in this competition is not only for my passion in motorsports but also for the opportunity to gain hands on experience to the challenges that faces modern day engineers. This year’s competition has once again demonstrated this. I am please to have lead the team to achieve 12th overall with 66 teams taking part this year. It is my hope that the competition will no longer be a virtual event and our team to achieve even more impressive results!”
Yeung Chun Hong Jasper, Team captain
Payload Challenge 5 of British Model Flying Association 2019 University and Schools Flight Challenges
This article appears in the news from the HKU Engineering Faulty website
Three “Design, Build and Fly” teams from the Department of Mechanical Engineering dominated the Payload Challenge 5 of the British Model Flying Association (BMFA) 2019 University and Schools Flight Challenges. They won the champion, 1st runner-up and 3rd runner-up respectively after three days of competition.
The British Model Flying Association 2019 University and Schools Flight Challenges was held in BMFA Buckminster, Sewstern Lane, Grantham, Lincolnshire, NG33 5RW from May 31 to June 2, 2019. With the technical support from the Hong Kong Air Cadet Corp (HKACC) and the Hong Kong Model Engineering Club Limited (HKMEC), our teams competed the 2019 Payload Challenge 5 with other 14 teams from all over the world, including UK and USA.
Competing teams were required to design and build a radio controlled (RC) aircraft using the specified design and equipment parameters, capable of carrying the specified liquid payload. Contestants should design their aircraft to maximise the value of the ratio “payload/aircraft empty mass”. Apart from submitting a technical report for the aircraft’s design and construction with design drawings and a verbal presentation, teams were required to complete three rounds of flight missions. Each aircraft was required to complete a flight without any payload in the first round. Then the payload was increased to 2kg and 4kg in the second and third round respectively. After three days of competition, our teams completed all three missions successfully and team #4, #3 and #2 won the champion, 1st runner-up and 3rd runner-up respectively.
Dr C.K Chan, supervisor of the teams, was proud of the excellent performance of the teams. He remarked, “It was not only a competition, but also an eye-opening experience for the students. They had chances to communicate and exchange ideas with other teams on design, selection of propellers, validity of different CAD software, weight minimization methods, payload loading and unloading mechanism, sourcing of components, etc. We are grateful to have such valuable experience and we thank the University for supporting us. ”