- kit
- April 26, 2019
- 7:33 pm
Project descriptions
Team information
Project leader: Zhang Tianyi, BEng(ME)
Team member(s): Tao Yufu, BEng(ME); XU Wenyutian, BEng(ME); Tsang Ho-Yin, BEng(ME)
Dr. Wang Z. (Department of Mechanical Engineering)
The topic of the project is “Surgical robotic system development for dental applications”.
A group of four students were dedicated to making a compact and dexterous dental robot specially designed for private dental clinics at densely populated cities like Hong Kong. Tendon-driven mechanism is adopted to minimize its size while a six Degree-of-Freedom mechanism in its joints helps boosting its dexterity. A haptic device was utilized to translate the hand motions of the dentist for teleoperation.
The students started from literature review, all that way to the prototyping of the manipulator and system control programming. After a number of experiments conducted to examine the system characteristics including hysteresis and linearity of the system, a revised prototype was built to better meet the requirements for real dental applications.
Students could learn the fundamental concept of robotic manipulator. They would have hands-on experience to building hardwares and using 3D printing technology to manufacture the computer-aided designs. Besides, they could also get familiar with the kinematics analysis of a complex robotic manipulator. Both the forward and inverse kinematics would be introduced and explained. Moreover, the ability of making professional engineering drawings and C++ programming skills would also be well cultivated.
This project aimed to build a prototype of a tendon-driven robotic manipulator for dental applications. A robotic system was developed based on the master-slave mechanism. The development of the robotic system included designing and prototyping of a 6 Degree-of-Freedom robotic manipulator, programming of an operator console and actuation of motors. The mechanical designs of the manipulator was first built and then fabricated by 3D printing technology. Meanwhile, the inverse kinematics algorithm was established through D-H modeling and was then implemented onto the operator console. Finally, the system characteristics were analyzed with multiple experiments. Throughout the whole design process, MATLAB was frequently used to simulate the kinematic properties of the manipulator and verify the inverse kinematics algorithms.
This project is in the second phase following the success of previous student group, and it is expected to last for a lot more years to come. For mechanical engineering undergraduate students, it is a challenging task to develop a multi-joints robotic manipulator, due to the complexity of the manipulator and the students’ limited knowledge and experience. Also, the core theory involved in this project, namely the kinematics of a multi-joint manipulator, is not covered in the syllabus of mechanical engineering programme in HKU. This project provides a golden opportunity to students who are interested in Robotics and are planning to pursue advanced automatic control in their graduate studies. Moreover, the programming skills involved in this project are also essential to students who major in computer sciences.
There are altogether three things deemed challenging in this project. The first one is improvisation. As mechanical engineering students, we had far less experience on hands-on projects that were heavily relying on our academic knowledge gathered from books and lessons, so each of us was required to apply what was learnt with creativity to come up with this particular solution or design in the project.
The second challenge is integration. As the project was mainly categorized into two sections, namely hardware and software, and they were interconnected with each other so it was a chase with time to develop both parts simultaneously to facilitate the testing and calibration between them, which requires high level of collaboration and high degree of self-motivation for each member in the group to accomplish.
Last but not least, the urge for perfection had become an obstacle itself. Many iterations of designs and products were made due to defects observed among its preliminary prototypes, therefore numerous tweaks and changes were made which almost led to failure in delivering the final product at the later stage of the project. It is understandable for everyone to have wanted to push the limits and build up a perfect masterpiece, however in reality that is nearly impractical. It is crucial for the team to come up with a standard as to what level of completion of the prototype is fully satisfactory.
Based on product design and development, this project drives the students not only to consider design constraints thoroughly and practise prototyping skills with their own designs, but also requires them to initiate computer simulations to observe the product performance to validate the design and come up with solutions from defects found in a trial-and-error approach.
The purpose of the project is not solely limited to building a robotic manipulator that could track the dentist’s hand motions, it is also of vital importance that the surgical robotic system could become a solution towards labour shortage in the near future by providing equal access to high quality dental health care service for people living in rural areas, the elderly, as well as people with disabilities.
Therefore, while students are working on the project, they could understand the motivation behind and appreciate the bright future of medical robotic system in hopes of improving humans’ quality of life.
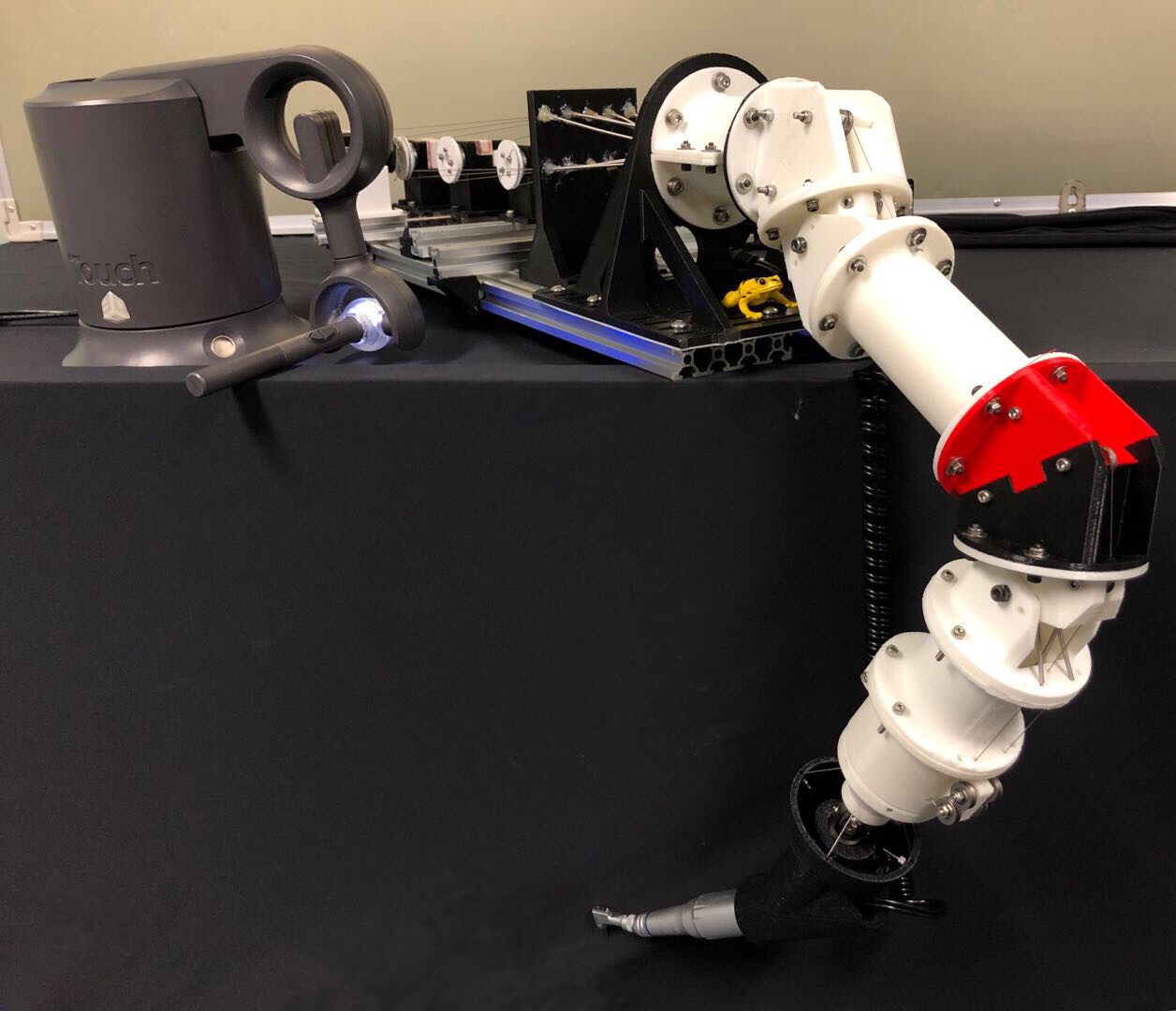
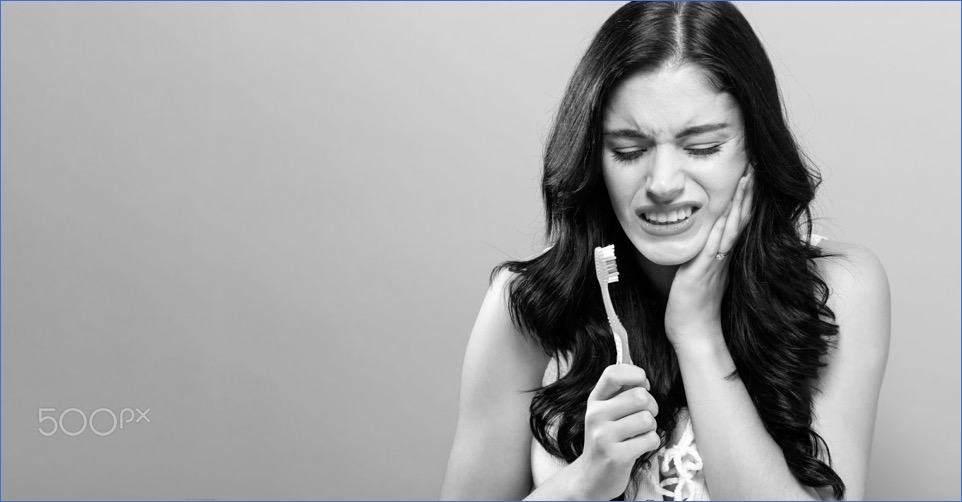